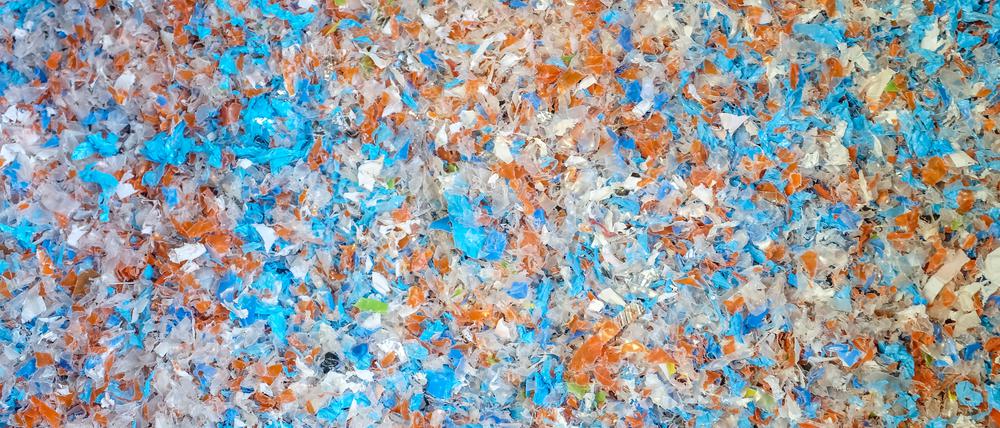
© Getty Images/© Santiago Urquijo
Schätze im Müll: Chemieprodukte aus Abfall statt aus Erdöl
Ein Großteil des Kunststoffmülls landet auf Deponien oder wird verbrannt. Zwei Forschungsteams haben nun Verfahren vorgestellt, mit denen aus den Abfällen hochwertige chemische Bausteine werden.
Das Recycling vieler Kunststoffabfälle ist noch immer schwierig, weshalb weltweit der Großteil auf Deponien landet oder, wie in Deutschland, verbrannt wird. Nun schlagen zwei Forschergruppen aus den USA für zwei mengenmäßig bedeutende Plastikarten ein Upcycling vor. Dabei werden die Polymere in höherwertige Chemikalien, darunter Tenside umgewandelt, die zur Herstellung von Seife und Waschmitteln verwendet werden können.
Polyethylen (PE) und Polypropylen (PP) zählen zu den am häufigsten eingesetzten Polymermaterialien und machen knapp die Hälfte der globalen jährlichen Kunststoffproduktion aus. Aus ihnen werden Plastiktüten, Folien, Milch- und Shampooflaschen, Cremetuben, Rohre, Spielzeug und einiges mehr hergestellt. Nicht wenig davon landet nach kurzer Gebrauchsdauer wieder im Müll. Vielfach gelingt es dann nicht, diese Kunststofftypen zu recyceln – stattdessen werden sie häufig verbrannt. Das liefert zwar noch Energie, setzt allerdings auch Kohlendioxid frei. Besser wäre es, das Material direkt im Wertstoffkreislauf zu halten.
Wie das aussehen kann, haben jetzt zwei Forschungsgruppen aus den USA im Fachmagazin „Science“ vorgestellt. Die eine um George Huber von der Universität Wisconsin speist PE und PP in einen Reaktor ein und erhitzt diesen unter Luftabschluss auf 500 Grad. Weil Sauerstoff fehlt, findet dabei keine Verbrennung, sondern eine sogenannte Pyrolyse statt. Deren Ergebnis, das Pyrolyse-Öl, ist ein Gemisch aus flüssigen Kohlenwasserstoffen.
Die Pyrolyse von Kunststoffabfällen ist industriell bereits im Einsatz. Neu am Ansatz der US-Forscher ist, dass sie den hohen Anteil an Substanzen mit Kohlenstoff-Kohlenstoff-Doppelbindungen im Pyrolyse-Öl für weitere chemische Umsetzungen nutzen. Auf die Art gelangen sie zu industriell wichtigen Substanzgruppen wie Aldehyden, Alkoholen, Carbonsäuren oder Aminen.
Die Autoren heben hervor, insbesondere wirtschaftlich besonders interessante Substanzklassen wie Mono- und Di-Aldehyde sowie Mono- und Dialkohole gewinnen zu können. Letztere seien hochpreisige Ausgangsstoffe für die Produktion von Polyestern und Polyurethanen. Kevin Van Geem vom Zentrum für nachhaltige Chemie an der Universität Gent in Belgien fügt in einem Kommentar hinzu, dass die derartige Gewinnung dieser Ausgangsstoffe im Vergleich zur herkömmlichen, petrochemischen Route zugleich rund 60 Prozent weniger Treibhausgase freisetzen würde.
Der zweite vorgestellte Ansatz zielt ebenfalls darauf, PE- und PP-Abfälle in nützliche Komponenten zu überführen. Konkret stellen die Autoren um Guoliang Liu von der Virginia Polytechnic Institute and State University mit ihrem Verfahren Fettsäure-Salze her, die als Tenside in Seifen, Shampoos oder Waschmitteln dienen – und bisher weitgehend auf fossilen Rohstoffen basieren. Ähnlich wie bei den Kollegen in Wisconsin werden die PE- und PP-Abfälle dafür zunächst in einem Reaktor erhitzt – in diesem Falle auf 360 Grad – und im Laufe eines chemischen Prozesses am Ende in Fettsäure-Salze umgewandelt.
Teure Trennung von Kunststoffarten könnte überfällig werden
Auch dieses Verfahren wird von den Autoren als potenziell wirtschaftlich beschrieben. So sei der Marktpreis der gewonnenen Tenside etwa dreimal so hoch wie der von Polyethylen – eine Wertsteigerung, die die Verfahrenskosten schnell kompensieren würde. Die Gruppe hatte die Technik zunächst für reines PE entwickelt, dann aber zeigen können, dass sie auch für PP und für PE-PP-Gemische funktioniert. Ein großer Vorteil, weil es damit überflüssig werde, PE und PP voneinander zu trennen, so die Autoren, was mitunter eine technische Herausforderung sei.
Gut 350 Millionen Tonnen größtenteils Erdöl-basierte Kunststoffe fallen laut eines OECD-Reports jährlich weltweit als Abfall an. Davon werden laut Report gerade einmal neun Prozent recycelt, also stofflich wieder- oder weiterverwertet. In Deutschland lag die entsprechende Quote im Jahr 2021 der von Branchenverbänden in Auftrag gegebenen „Conversio“-Studie zufolge immerhin bei rund einem Drittel, während 66 Prozent thermisch verwertet wurden. Das bedeutet, dass der Abfall verbrannt und die dabei entstehende Energie genutzt wird.
Als beste Lösung gilt indes das mechanische Recycling, bei dem gereinigte Abfälle ohne chemische Veränderung direkt wiederverwendet werden können. Allerdings muss das Ausgangsmaterial dafür sortenrein sein, was oft nicht der Fall ist. Für diese Anteile bleibt das chemische Recycling, bei dem die Polymere entweder in ihre Bausteine zerlegt oder – wie in den hier vorgestellten Verfahren – zur Synthese anderer Materialien genutzt werden.
Kevin Van Geem schätzt, dass dies langfristig für über 65 Prozent der Plastikabfälle das Verfahren der Wahl sein werde. Der Chemieingenieur weist in seinem Kommentar darauf hin, dass es üblicherweise mindestens fünf weitere Jahre dauere, ehe neu vorgestellte Verfahren industriell zum Einsatz kämen. Er schreibt: „Dennoch dürften innovative Technologien, die auf das Recycling von Kunststoffabfällen abzielen, die Kreislaufwirtschaft in der chemischen Industrie in den kommenden Jahren erheblich verbessern.“
- showPaywall:
- false
- isSubscriber:
- false
- isPaid:
- showPaywallPiano:
- false